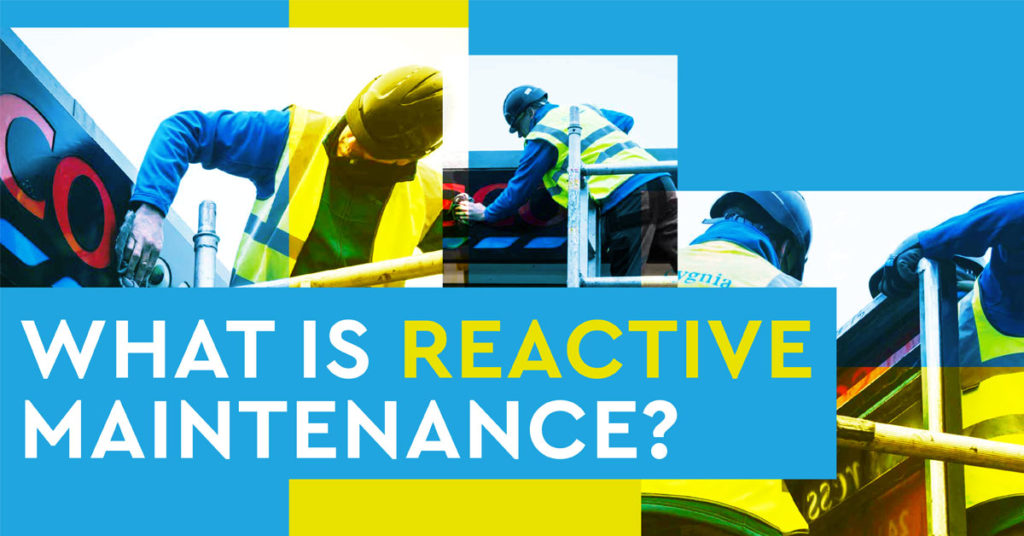
Cygnia provides signage maintenance in two forms; reactive and proactive. For this article we cover what reactive maintenance is, with the possible benefits and drawbacks you could receive.
In just about every facet of your life you have to deal with some form of maintenance. This holds true whether you own a house, drive a car, even if you have hair on your head. We’ll take a look at the two approaches to upkeep, starting below with reactive maintenance. You can consider the reasons why, and why not, this is an option for you.
What is Reactive Maintenance?
Reactive maintenance is where you repair or replace assets after they have failed or are starting to fail. This approach is very straightforward. You simply wait for the item to stop doing the job it is intended to do, look into why it has stopped. Then you take steps to either get the item to resume working once again.
Reactive maintenance is an approach we all take in certain cases. Light bulbs are a good example here – you install them and then wait for them to fail. When the bulb eventually stops working you know the problem is most likely to be with the bulb itself. And you know what the answer to the problem is – a new lightbulb.
In the case of the light bulb failing, that could be almost immediately or many months later. But the fault is easy to spot and quick to resolve. And as reactive maintenance is fundamentally repair-when-it-goes-wrong, it means your premises remain open for customers for as long as you want. You save money by only repairing problems when they arise.
In the case of your signage, reactive maintenance may be an attractive option. After all, you can readily see if something like a light has failed or the sign itself is no longer fitted level and straight. So they can appear to be a simple part of your store’s fixings which don’t require extensive investigation.
However, the reality can be quite different.
Reactive Maintenance – The Drawbacks
While your signage may look simple and have no moving parts (if it does then we’d love to see it), it is still fixed to the front of your premises and – if lit – contains electrical components. Also, it may contain adhesive films or made using adhesives instead of fixings. Let’s look at these in turn.
If your signage falls away from the facia, it could be due to the fixings failing. This can cause damage to the signage itself along with the frontage of your store. This would place your staff and customers at risk. It can also potentially result in repairs taking significant time to sort out. It could even mean your signage needing replacing – wiping out any cost savings.
Similarly, if lights fail this may not be due to them reaching the end of their lifecycle. Instead it could be down to connectivity or other componentry issues. Then, a simple bulb or tube replacement won’t resolve the issue. You will risk spending money again sooner than you expect on replacing it. If the issue is more serious, then you could even be at risk of electrical problems within your premises. It could even become a fire risk.
Finally, components within your signage can have their lifespan limited by the environment they are exposed to. For example, a plastic film on your signage may deteriorate when subjected to a combination of seasonal weather and UV light. It will fade, become brittle, or start to come away from the signage itself. While this is usually a gradual process, with reactive maintenance you won’t become aware of the problem until it become evident and unsightly. Making your signage appear in poor condition, reflecting badly on your business.
Summary
As you can see, reactive maintenance is a viable option to take with your signage but does carry with it some risk. Repairing or replacing items as they fail is a normal and accepted route, but you should consider carefully if reactive maintenance is the best option for you. We have previously written about proactive maintenance which is worth comparing to give you a broad picture of the best option for you and your signage maintenance needs.